Za promatranje zamornog loma i analizu mehanizma loma korišten je skenirajući elektronski mikroskop; u isto vrijeme, ispitivanje zamora na savijanje centrifugiranjem provedeno je na razugljičenim uzorcima pri različitim temperaturama kako bi se usporedio vijek trajanja ispitivanog čelika sa i bez odugljičenja i analizirao učinak odugljičenja na performanse zamora ispitivanog čelika. Rezultati pokazuju da, zbog istovremenog postojanja oksidacije i dekarburizacije u procesu zagrijavanja, interakcija između njih, što rezultira debljinom potpuno dekarburiziranog sloja s porastom temperature pokazuje trend povećanja, a zatim smanjenja, debljina potpuno deugljičenog sloja doseže najveću vrijednost od 120 μm na 750 ℃, a debljina potpuno deugljičenog sloja doseže minimalnu vrijednost od 20 μm na 850 ℃, a granica zamora ispitivanog čelika je oko 760 MPa, i izvor pukotina uslijed zamora u ispitivanom čeliku uglavnom su nemetalni uključci Al2O3; ponašanje kod dekarburizacije uvelike smanjuje vijek trajanja ispitivanog čelika od zamora, utječući na učinak testnog čelika od zamora, što je deblji sloj dekarburizacije, to je niži vijek trajanja od zamora. Kako bi se smanjio utjecaj sloja za odugljičenje na performanse zamora ispitnog čelika, optimalna temperatura toplinske obrade ispitnog čelika trebala bi biti postavljena na 850 ℃.
Oprema je važna komponenta automobila,zbog rada pri velikoj brzini, zahvatni dio površine zupčanika mora imati visoku čvrstoću i otpornost na abraziju, a korijen zuba mora imati dobru izvedbu zamora savijanjem zbog konstantnog opetovanog opterećenja, kako bi se izbjegle pukotine koje dovode do materijala prijelom. Istraživanja pokazuju da je odugljičenje važan čimbenik koji utječe na zamor metalnih materijala savijanjem pri centrifugiranju, a učinak pri zamoru pri savijanju pri centrifugiranju važan je pokazatelj kvalitete proizvoda, stoga je potrebno proučiti ponašanje ispitnog materijala pri dekarburizaciji i zamor pri savijanju pri centrifugiranju.
U ovom radu, peć za toplinsku obradu na 20CrMnTi zupčaniku čeličnu površinu decarburization test, analizira različite temperature zagrijavanja na ispitnom čeličnom decarburization sloju dubine promjenjivog zakona; pomoću QBWP-6000J jednostavnog stroja za ispitivanje zamora grede na ispitivanju zamora rotacijskim savijanjem ispitnog čelika, određivanje performansi zamora ispitnog čelika, te u isto vrijeme za analizu utjecaja dekarburizacije na performanse zamora ispitnog čelika za poboljšanje stvarne proizvodnje proces proizvodnje, poboljšati kvalitetu proizvoda i pružiti razumnu referencu. Učinkovitost ispitivanja zamora čelika određena je strojem za ispitivanje zamora na savijanje vrtnjom.
1. Ispitni materijali i metode
Ispitni materijal za jedinicu koja daje 20CrMnTi čelik za zupčanike, glavni kemijski sastav kao što je prikazano u tablici 1. Test dekarburizacije: ispitni materijal se obrađuje u cilindrični uzorak F8 mm × 12 mm, površina bi trebala biti svijetla bez mrlja. Peći za toplinsku obradu su zagrijane na 675 ℃, 700 ℃, 725 ℃, 750 ℃, 800 ℃, 850 ℃, 900 ℃, 950 ℃, 1000 ℃, u uzorku i držane 1 sat, a zatim ohlađene na zraku do sobne temperature. Nakon toplinske obrade uzorka stvrdnjavanjem, brušenjem i poliranjem, s 4% otopinom dušično-alkoholne erozije, korištenjem metalurške mikroskopije za promatranje ispitnog sloja dekarburizacije čelika, mjerenje dubine sloja dekarburizacije pri različitim temperaturama. Ispitivanje zamora na savijanje centrifugiranjem: ispitni materijal prema zahtjevima obrade dviju skupina uzoraka zamora na savijanje centrifugiranjem, prva skupina ne provodi ispitivanje dekarburizacije, druga skupina test dekarburizacije na različitim temperaturama. Korištenje stroja za ispitivanje zamora na savijanje centrifugiranjem, dvije skupine ispitnog čelika za ispitivanje zamora na savijanje centrifugiranjem, određivanje granice zamora dviju skupina ispitnog čelika, usporedba vijeka trajanja dviju skupina ispitnog čelika na zamor, korištenje skeniranja promatranje loma od zamora elektronskim mikroskopom, analizirati razloge loma uzorka, istražiti učinak dekarburizacije na svojstva zamora ispitivanog čelika.
Tablica 1 Kemijski sastav (maseni udio) ispitivanog čelika težinski %
Utjecaj temperature zagrijavanja na dekarburizaciju
Morfologija organizacije dekarburizacije pri različitim temperaturama zagrijavanja prikazana je na slici 1. Kao što se može vidjeti sa slike, kada je temperatura 675 ℃, na površini uzorka ne pojavljuje se sloj dekarburizacije; kada temperatura poraste na 700 ℃, počeo se pojavljivati površinski sloj za dekarburizaciju uzorka, za tanki feritni sloj za dekarburizaciju; s porastom temperature do 725 ℃, debljina sloja za dekarburizaciju površine uzorka značajno se povećala; 750 ℃ debljina sloja dekarburizacije doseže svoju maksimalnu vrijednost, u ovom trenutku, feritno zrno je jasnije, grublje; kada temperatura poraste na 800 ℃, debljina sloja za dekarburizaciju počela se značajno smanjivati, njegova debljina je pala na polovicu od 750 ℃; kada temperatura nastavi rasti do 850 ℃, a debljina dekarburizacije prikazana je na slici 1. 800 ℃, puna debljina sloja dekarburizacije počela se značajno smanjivati, njegova debljina je pala na 750 ℃ kada je polovica; kada temperatura nastavi rasti do 850 ℃ i više, debljina sloja pune dekarburizacije ispitivanog čelika nastavlja se smanjivati, debljina sloja polovine dekarburizacije počela se postupno povećavati sve dok morfologija sloja pune dekarburacije nije potpuno nestala, morfologija sloja polovine dekarburacije postupno se čisti. Može se vidjeti da je debljina potpuno razugljičenog sloja s porastom temperature prvo povećana, a zatim smanjena, razlog za ovu pojavu je zbog ponašanja uzorka u procesu zagrijavanja u isto vrijeme oksidacije i dekarburizacije, tek kada brzina dekarburizacije je brža od brzine oksidacije pojavit će se fenomen dekarburizacije. Na početku zagrijavanja, debljina potpuno dekarburiziranog sloja postupno se povećava s porastom temperature sve dok debljina potpuno dekarburiziranog sloja ne dosegne maksimalnu vrijednost, u ovom trenutku za nastavak podizanja temperature, stopa oksidacije uzorka je brža od stopu dekarburizacije, koja sprječava povećanje potpuno dekarburiziranog sloja, što rezultira silaznim trendom. Može se vidjeti da je, unutar raspona od 675 ~950 ℃, vrijednost debljine potpuno dekarburiziranog sloja na 750 ℃ najveća, a vrijednost debljine potpuno dekarburiziranog sloja na 850 ℃ najmanja, stoga se preporučuje da temperatura zagrijavanja čelika za ispitivanje bude 850 ℃.
Slika 1. Histomorfologija dekarburiziranog sloja ispitnog čelika držanog na različitim temperaturama zagrijavanja 1 sat
U usporedbi s polu-dekarburiziranim slojem, debljina potpuno dekarburiziranog sloja ima ozbiljniji negativan utjecaj na svojstva materijala, uvelike će smanjiti mehanička svojstva materijala, poput smanjenja čvrstoće, tvrdoće, otpornosti na trošenje i granice zamora , itd., a također povećavaju osjetljivost na pukotine, utječući na kvalitetu zavarivanja i tako dalje. Stoga je kontrola debljine potpuno dekarburiziranog sloja od velike važnosti za poboljšanje učinka proizvoda. Na slici 2 prikazana je krivulja varijacije debljine potpuno razugljičenog sloja s temperaturom, koja jasnije prikazuje varijaciju debljine potpuno razugljičenog sloja. Na slici se može vidjeti da je debljina potpuno dekarburiziranog sloja samo oko 34 μm na 700 ℃; s porastom temperature do 725 ℃, debljina potpuno dekarburiziranog sloja značajno se povećava na 86 μm, što je više od dva puta debljine potpuno dekarburiziranog sloja na 700 ℃; kada se temperatura podigne na 750 ℃, debljina potpuno dekarburiziranog sloja Kada temperatura poraste na 750 ℃, debljina potpuno dekarburiziranog sloja doseže maksimalnu vrijednost od 120 μm; kako temperatura nastavlja rasti, debljina potpuno dekarburiziranog sloja počinje se naglo smanjivati, na 70 μm na 800 ℃, a zatim na minimalnu vrijednost od oko 20 μm na 850 ℃.
Slika 2. Debljina potpuno dekarburiziranog sloja pri različitim temperaturama
Učinak dekarburizacije na performanse zamora kod savijanja centrifugiranjem
Kako bi se proučio učinak odugljičenja na svojstva zamora čelika za opruge, provedene su dvije skupine ispitivanja zamora na savijanje centrifugom, prva skupina je bila ispitivanje zamora izravno bez odugljičenja, a druga skupina je bila ispitivanje zamora nakon odugljičenja pri istom naprezanju. (810 MPa), a proces dekarburizacije je održan na 700-850 ℃ 1 h. Prva skupina uzoraka prikazana je u tablici 2, a to je vijek trajanja opružnog čelika od zamora.
Dugotrajnost prve skupine uzoraka prikazana je u tablici 2. Kao što se može vidjeti iz tablice 2, bez dekarburizacije, ispitivani čelik je bio podvrgnut samo 107 ciklusa pri 810 MPa, i nije došlo do loma; kada je razina naprezanja premašila 830 MPa, neki su se uzorci počeli lomiti; kada je razina naprezanja premašila 850 MPa, svi su uzorci zamora bili slomljeni.
Tablica 2. Otpornost na zamor pod različitim razinama naprezanja (bez dekarburizacije)
Za određivanje granice zamora koristi se grupna metoda za određivanje granice zamora ispitivanog čelika, a nakon statističke obrade podataka granica zamora ispitivanog čelika iznosi oko 760 MPa; kako bi se okarakterizirao vijek trajanja ispitivanog čelika na zamor pod različitim naprezanjima, nacrtana je SN krivulja, kao što je prikazano na slici 3. Kao što se može vidjeti na slici 3, različite razine naprezanja odgovaraju različitom vijeku trajanja na zamor, kada vijek trajanja na zamor od 7 , što odgovara broju ciklusa za 107, što znači da je uzorak pod ovim uvjetima u stanju prolaznosti, odgovarajuća vrijednost naprezanja može se aproksimirati kao vrijednost čvrstoće na zamor, to jest 760 MPa. Može se vidjeti da S - N krivulja važna za određivanje vijeka trajanja materijala od zamora ima važnu referentnu vrijednost.
Slika 3 SN krivulja eksperimentalnog ispitivanja zamora čelika rotacijskim savijanjem
Dugotrajnost druge skupine uzoraka prikazana je u tablici 3. Kao što se može vidjeti iz tablice 3, nakon što je ispitivani čelik razugljičen na različitim temperaturama, broj ciklusa je očito smanjen i iznosi više od 107, a svi zamorni uzorci su slomljeni, a vijek trajanja zamora je znatno smanjen. U kombinaciji s gore navedenom debljinom dekarburiziranog sloja s krivuljom promjene temperature može se vidjeti, debljina dekarburiziranog sloja od 750 ℃ najveća je, što odgovara najnižoj vrijednosti vijeka trajanja od zamora. Debljina dekarburiziranog sloja od 850 ℃ najmanja je, što odgovara relativno visokoj životnoj vrijednosti zamora. Može se vidjeti da ponašanje dekarburizacije uvelike smanjuje performanse materijala na zamor, a što je deblji dekarburizirani sloj, to je niži vijek trajanja od zamora.
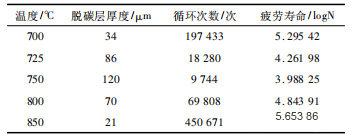
Tablica 3. Otpornost na zamor pri različitim temperaturama dekarburizacije (560 MPa)
Morfologija loma uzorka uslijed zamora promatrana je skenirajućim elektronskim mikroskopom, kao što je prikazano na slici 4. Na slici 4(a) za područje izvora pukotine, na slici se može vidjeti očiti luk zamora, prema luku zamora kako bi se pronašao izvor zamora, može se vidjeti, izvor pukotine za "riblje oko" nemetalne inkluzije, inkluzije na lako izazvati koncentraciju naprezanja, što rezultira pukotinama uslijed zamora; Slika 4(b) za morfologiju područja proširenja pukotine, mogu se vidjeti očite trake zamora, raspodjela poput rijeke, pripada kvazi-disocijativnom lomu, s pukotinama koje se šire, što na kraju dovodi do loma. Slika 4(b) prikazuje morfologiju područja širenja pukotine, mogu se vidjeti očite pruge zamora, u obliku riječne raspodjele, koja pripada kvazi-disocijativnom lomu, a uz kontinuirano širenje pukotina, što u konačnici dovodi do loma .
Analiza zamornog loma
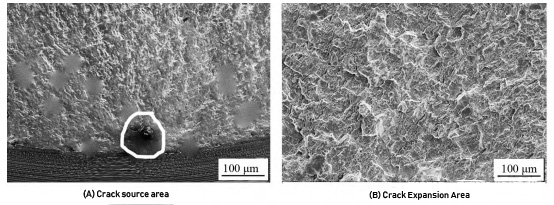
Slika 4 SEM morfologija zamorne lomne površine eksperimentalnog čelika
Kako bi se odredio tip uključaka na slici 4, provedena je analiza sastava energetskog spektra, a rezultati su prikazani na slici 5. Može se vidjeti da su nemetalni uključci uglavnom Al2O3 uključci, što ukazuje da su uključci glavni su izvor pukotina uzrokovanih pucanjem inkluzija.
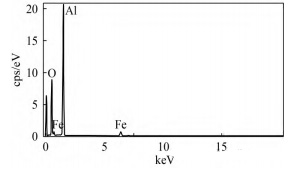
Slika 5 Energetska spektroskopija nemetalnih uključaka
Zaključiti
(1) Postavljanjem temperature zagrijavanja na 850 ℃ minimizirat će se debljina dekarburiziranog sloja kako bi se smanjio učinak na performanse zamora.
( 2) Granica zamora ispitnog čelika pri savijanju vrtnjom je 760 MPa.
( 3 ) Ispitivanje pucanja čelika u nemetalnim uključcima, uglavnom smjesi Al2O3.
(4) dekarburizacija ozbiljno smanjuje vijek trajanja ispitivanog čelika od zamora, što je deblji sloj dekarburizacije, to je niži vijek trajanja od zamora.
Vrijeme objave: 21. lipnja 2024